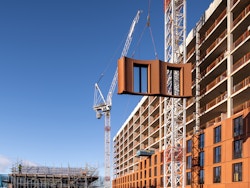
Site progress
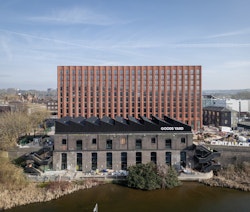
The Vaults opens out onto the Trent and Mersey canal
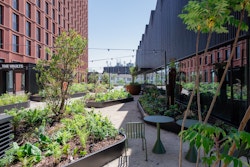
Fluted concrete panels viewed from the generous landscape amenity space
How Goods Yard is evoking the Potteries’ industrial past
I grew up in Wolverhampton, where you can still see the immense industrial wealth that used to flow through the town in the richly ornamented Victorian buildings. Many of these are now derelict, or underused.
It’s ironic because, as an architect, I know that no client would pay us to design buildings like those now. The time, labour and craftsmanship involved would just be too expensive. But I believe that even on a budget there are things we can do, by using modern methods of construction, to put some detail and interest back into buildings. We had an opportunity to do that when we were asked to design Goods Yard in Stoke-on-Trent.
As in many of these post-industrial towns, young people tend to move away from Stoke to where there are better opportunities. There isn’t the kind of exciting, new-build rental market that has developed in the trendier areas of bigger cities like Manchester and Birmingham. So when Stoke secured some levelling-up funding to redevelop the area around the station, part of the aim was to create homes for rent that would be attractive to young people – encouraging them to stay by providing affordable but high- quality places to live, from where they could easily commute to neighbouring cities.
Goods Yard is a mixed-use scheme located close to Stoke station, and right next to the Trent and Mersey Canal and the A500. The site used to be a busy interchange of materials and manufactured goods and the development repurposes a number of Victorian structures. Dominating the scheme, though, is a new, ten-storey block of 174 apartments for rent. At 76m long and 20m wide, its size and form are reminiscent of the mills and warehouses of the Victorian era.
The development had to work economically—rents here are not high—and we had to extract the utmost from our budget. Our approach was to keep the form very simple, with lots of repetition throughout the apartments and the core designs.
We started with an in-situ concrete frame, arranged on a 6m grid. This kept spans short and allowed us to save material (and carbon) by keeping the slabs slim. The concrete frame is also a very cost-effective way of dealing with fire protection and acoustics—vital considerations in a residential building.
That left enough budget to do something interesting with the facade. It is built from 360 terracotta-coloured precast concrete panels, the vast majority of which are made from just three mould shapes, corresponding to the lower floor, middle floors and top floor. The only exceptions were the corners, which have a special edge piece cast onto the regular panel. Each panel weighs approximately 7 tonnes.
I felt that the building would mainly be viewed from two perspectives: by people passing it at an average of 50mph in a car or a train, but also by pedestrians who would have a closer, slower experience. For the former, we created the scalloped shape of the facade panels. These are 6m x 3m, so even from a distance, or when passing quickly, the repeated shape provides shadows and interest. Then, for the pedestrians, we introduced the vertical fluting in each panel, and this detail also responds to the light, creating shadows and texture.
Of course, this costs more than using plain, flat panels, but by keeping to a limited number of shapes we made it very efficient—the building was delivered for just £220 per ft2. The panels were fabricated by Techrete, which made the curved scallop shapes from reuseable timber formwork, and then lined it with off-the-shelf ribbed rubber mouldings to create the vertical grooves. Each panel arrived on site with windows, Juliet balconies and interior insulation fitted, cutting the trades required and site time significantly.
The concrete facade is coloured terracotta by the addition of iron oxide—so the colour is reminiscent both of local brick buildings and also the clay that made Stoke a historic centre of ceramics. But there is more going on here than just the colour. We’ve used the concrete something like the way that Josiah Wedgwood used clay to create high-quality ceramic pottery—complex, subtle shapes, designed to be reproduced in volume very efficiently. I think Wedgwood would understand what we’ve done here, and I hope he would approve.
This article was published in the summer 2025 issue of Concrete Quarterly.
Written on 30.06.2025, by Fraser Godfrey